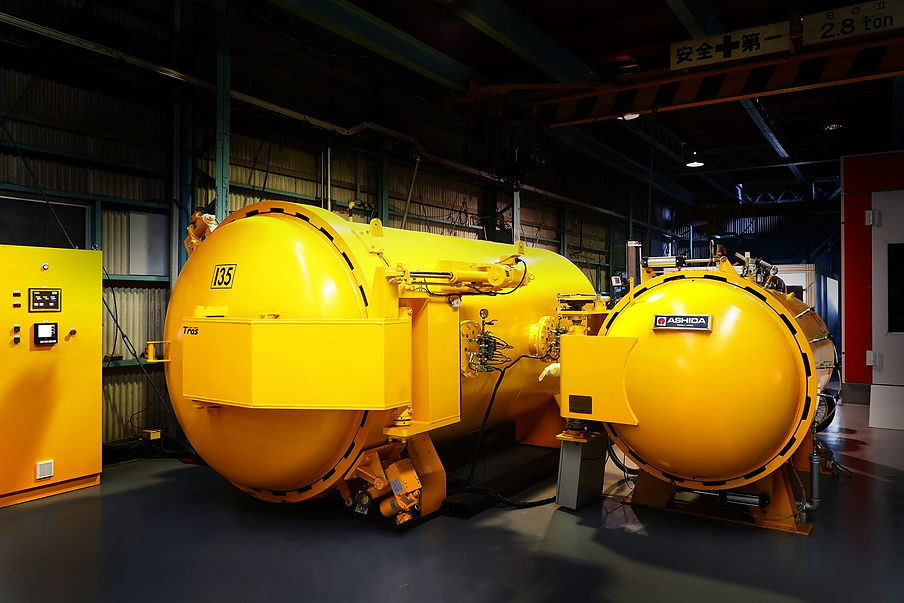
TECHNOLOGY
テクノロジー
What is advanced composite material ?
What is composite material?
A composite describes a material or product made by combining different materials. Since 1987, Tras has been producing light, strong, and beautiful "composite products" made of carbon and epoxy resin. The carbon composite is a so-called an advanced composite material. Tras attributes the origin of the composite molding technique to the Ashura statue, a national treasure that has remained unscathed for 1,300 years. The composite material made from flax and lacquer was molded in a process known as deactivated dry-lacquer molding. This process, which combines different materials to create a product, is truly a modern composite and molding technique. We believe that deactivated dry-lacquer molding itself is the root and model of composite molding. Tracing these roots, we have arrived at the idea that it may be possible to reduce the high CO2 emissions that are the only drawback of carbon. Carbon fiber, which is made from petroleum, has high CO2 emissions, but by replacing it with a new composite material called "natural fiber," which can be treated in the same way as carbon products, it is possible to reduce CO2 emissions by -85%. Tras will utilize its "accumulated skills" accumulated through over 30 years of manufacturing carbon products to "replace carbon fiber with natural fiber" and actively work on global warming countermeasures.
Comparison of material properties
The same composition (bending) as aluminum material (t10) is
Index of bending rigidity: E1 E: Modulus of elasticity I: Moment of inertia of area Plate I (per unit width) = t 3/12
The same strength (bending) as aluminum material (t10) is
Index of bending strength: σZ σ: strength Z: section modulus Z of plate material (per unit width) = t 2/6
The difference between "stiffness" and "strength" is based on the following criteria.
-
Rigidity: A measure of how difficult it is to deform a material when a certain force acts on it.
-
Strength (toughness): This is the limit of the force that a material can endure, at which it will not break.
Production of carbon fiber products
Carbon manufacturing process
How are composite products made at Tras? The general process of manufacturing prepreg carbon (dry carbon) is as follows:



PROJECT SUMMARY
Process Overview
-
In order to cut prepreg (intermediate material on a sheet of carbon fiber impregnated with thermoplastic resin), a paper pattern is created according to the manufacturing shape. After the paper pattern is converted into CAD data, it is cut by a dedicated plotter.
-
Molds are created for different purposes, such as molds, chemical molds, and prepreg female molds, and then prepreg is laminated to the molds. The process of attaching the prepreg to the mold is known as craftsmanship, and the direction of the fibers and the number of layers are determined based on strength calculations. In other words, it is possible to freely mold parts that need to be strong and parts that need to be flexible, and this is where the skill of the craftsman really comes into play.
-
The laminate is placed in a nylon backing film and sealed under true negative pressure (baking).
-
The product is then placed in an autoclave and pressurized and heated while the air in the backing film is evacuated with a vacuum pump.
-
Advantage: Because of the pressurization, the product becomes homogeneous with low residual porosity, resulting in a high-quality product.
Disadvantage of the autoclave: Since each piece is handmade, it is not suitable for mass-production and productivity is low. Therefore, CFRP is for high-mix low-volume production, and the prototype and high-value-added product markets are the best places to work.